6.4.2 裂纹扩展模拟
6.4.2.1 有限板单边裂纹扩展
设有一单轴均匀受拉方板[见图6.9(a)],板边长均为16 cm。板左侧有一直裂纹。方板位置x∈[0,16],y∈[-8,8],初始裂纹坐标(0.0,1.0),(7.0,1.0),均布荷载T=1 MPa;固定左侧底角点(0,-8)。方板材料参数:E=1000 MPa,泊松比v=0.3。方板上共离散31×31 个节点,6×6 高斯积分,围线积分区域为a/3×a/3。断裂韧度KC 取一小值,扩展步长为0.5,共模拟5 步。为了验证水平集更新算法,与扩展有限元(XFEM)[123]的计算结果进行了比较。表6.3 给出了每步扩展前XFEM 与耦合法的计算的SIFs;表6.4 比较了两种方法在裂纹扩展过程中确定的裂尖坐标。两种方法吻合得非常好,说明本文所提出的水平集更新算法能够准确地追踪裂纹的位置。由于裂纹并不处于试样的对称位置,因此KII不为0。但又由于KI远远大于KII且KI逐步增大而KII逐步减小,因此整个开裂过程表现为I 型扩展。
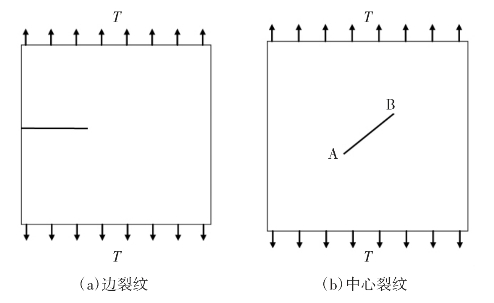
图6.9 含裂纹方板
表6.3 单边裂纹应力强度因子/(MPa·cm1/2)
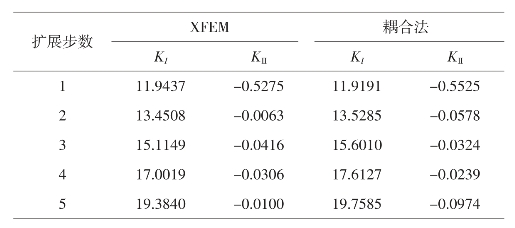
表6.4 单边裂纹尖端位置/(cm)
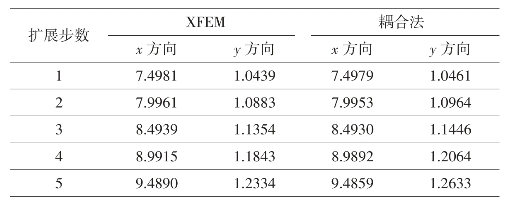
6.4.2.2 中心裂纹扩展
该算例中[见图6.9(b)],方板及其材料参数均与例6.5.1 中相同。中心裂纹的两个裂纹尖端坐标分别为(5,-1)和(11,1)。表6.5、表6.6 分别给出了XFEM[123]与PUEM 在中心裂纹扩展过程中应力强度因子和裂尖位置的计算结果。可以看出,裂纹扩展过程中KI逐步增大,KII逐步减小并趋于0。裂纹扩展初期的KI与KII相差不大,但裂纹开裂后,KI要远远大于KII,说明在开裂初期,裂纹面受到拉剪应力的作用,表现为I、II 型复合开裂。而一旦裂纹发生扩展,则以I 型扩展为主并表现出失稳扩展的特点,最终导致试件的完全破坏。
表6.5 中心裂纹应力强度因子/(MPa·cm1/2)

表6.6 中心裂纹裂尖位置/(cm)
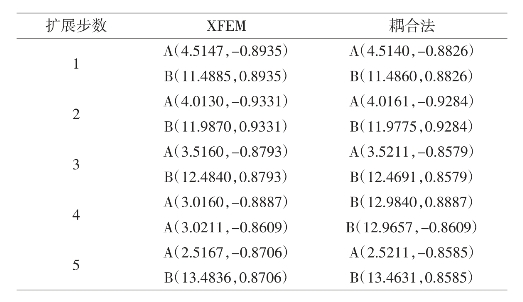
6.4.2.3 单边斜裂纹扩展
选取平板尺寸为10 cm×20 cm,左侧中点处有一与水平线呈40°,长度为2 cm 的斜裂纹[123](见图6.10),顶部和底部分别承受σ=40000 Pa 拉力作用。材料参数E=7400 MPa,v=0.3。在平板上共离散21×41 节点。断裂准则选取为最大周向拉应力准则,裂纹扩展步长为0.5 cm,断裂韧度KC=0.06 MPa/cm。本文共追踪9 步,裂纹扩展轨迹见图6.11。图6.11 为裂纹长度与应力强度因子KI、KII以及等效应力强度因子Keq的关系图。由图6.10、图6.11 可以看出,裂纹沿着与拉力几乎垂直的方向扩展,KI逐步增大,KII先增大后减小但其值非常接近0;裂纹扩展前期为复合型裂纹,后期则以I 型裂纹为主,一旦裂纹开裂,裂纹表现为不稳定扩展,直至最终破坏。
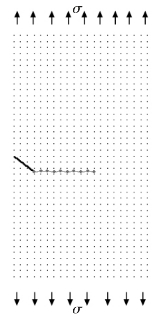
图6.10 单边斜裂纹扩展路径图
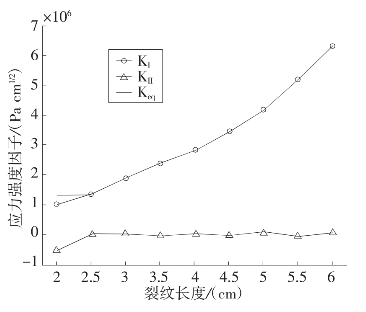
图6.11 单边斜裂纹应力强度因子
6.4.2.4 双悬臂梁裂纹扩展
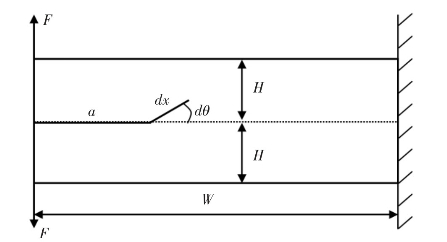
图6.12 双悬臂梁试件
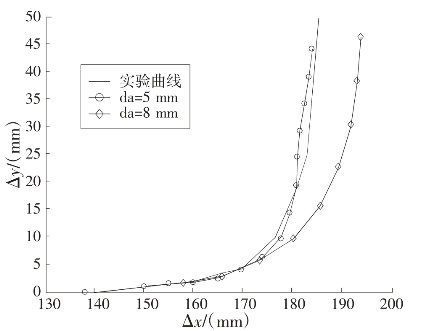
图6.13 不同扩展步长对应的扩展路径
试件如图6.12 所示,W=300 mm,H=50 mm,a=138 mm,F=100 N,Δx=12 mm,dθ=4.8°。按平面应力计算,弹性模量E=200 MPa,泊松比v=0.3。坐标系原点位于左侧边界中点,x 轴沿中线。Sumi 等[124]通过试验方法和有限元分别研究了该问题,指出裂纹扩展的曲线路径是不稳定的,或者向上或者向下。参考Fleming 等[11]的工作,在试样上共离散49×17 个节点,材料断裂韧度KC 取一较小值,分别模拟扩展步长da=5 mm 和da=8 mm 两种情况下裂纹的扩展路径。图6.13 给出两种扩展步长下裂纹扩展路径。可以看出,本文得到的扩展路径曲线相对比较光滑,且与试验曲线十分接近。图6.14 给出两种扩展步长情况下,裂纹扩展过程中SIF 的变化情况。可以看出,KI≫KII并且KI逐步增大,裂纹主要以I 型断裂为主。
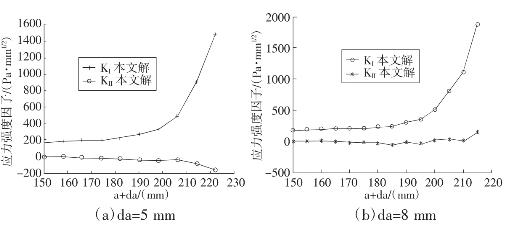
图6.14 裂纹扩展过程中的应力强度因子
6.4.2.5 节理岩体水力致裂模拟
本算例选取文献[125]中水压致裂的CT 试验的第3 层扫描剖面作为分析对象,假设其为具有均匀周边围压的平面应变问题,其几何模型如图6.15 所示。其材料常数为:R=25 mm,E=4860 MPa,v=0.2,a=4 mm。水压σ=4 MPa,围压p=2 MPa。考虑模型的对称性,取其一半进行准静态分析。裂纹尖端最大周向拉应力的测定值为σt=1.472 MPa。图6.16 给出了计算模型的节点分布。将内部水压力边界等分为21 段,外部围压边界分为88段,每个子段采用4 个高斯积分点。参考文献[126],裂纹每次扩展的步长取为da=2 mm,共模拟10 步。图6.17 为本文方法模拟的裂纹扩展路径。可以看出与图6.18 的试验结果[125]十分接近。
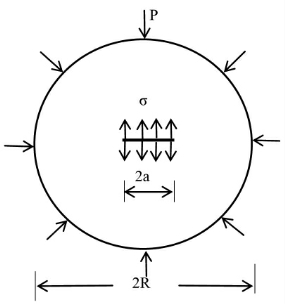
图6.15 CT几何模型及其边界
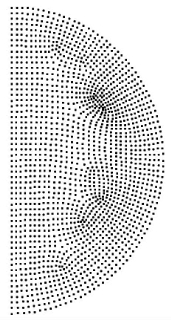
图6.16 节点分布

图6.17 本文方法模拟的右侧裂纹扩展路径
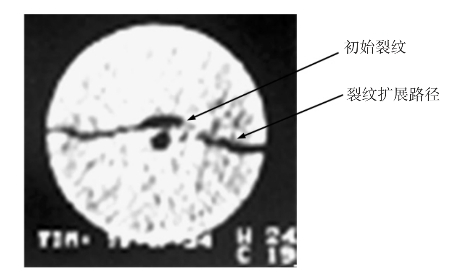
图6.18 试验得到的裂纹扩展路径[125]
6.4.2.6 含三个孔洞的三点弯梁的裂纹扩展模拟
三点弯曲梁中心线左侧含有三个小圆孔,其底部含有一条初始裂纹,裂纹几何位置依赖裂纹长度a 和裂纹到中心线的距离b(见图6.19)。考虑a 和b 选取两组不同值时裂纹的扩展路径(见表6.7)。
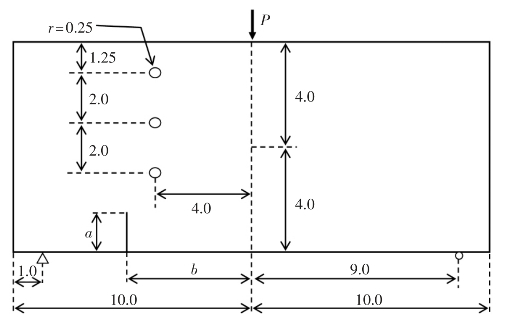
图6.19 含三个圆孔的三点弯曲梁试件
表6.7 三点弯曲梁的两种裂纹试样

Bittencourt 等[127]对该问题分别进行了试验和数值模拟。结果表明,初始裂纹的位置决定了裂纹扩展的路径,或是与孔洞相交或是从两个孔洞之间穿过。Tada 等[128]认为材料的弹性模量、泊松比和厚度可以任意选取,原因是在线弹性假设下决定裂纹扩展的应力强度因子与这些参数无关。在本文中E=199.95MPa,v=0.3,P=4450 N。在梁上共离散967 个节点,844 个四边形背景积分单元。图6.20 为第一种情况下本文方法、e-EFGM[129]和实验方法得到的裂纹扩展路径。从实验结果来看,裂纹从端部沿曲线从两个圆孔之间穿过并中止于中间孔洞。本文方法和e-EFGM 的模拟路径都和实验路径十分接近,但本文方法的扩展路径为曲线而e-EFGM 为直线。由于在孔边往往存在高的应力区,裂纹会向这些应力区弯折,最终形成曲线型扩展轨迹。因此,本文方法的计算结果更接近实验结果。图6.21 为第二种情况下本文方法、e-EFGM 模拟的裂纹扩展路径。两种方法的模拟路径很接近,与实验结论相吻合。
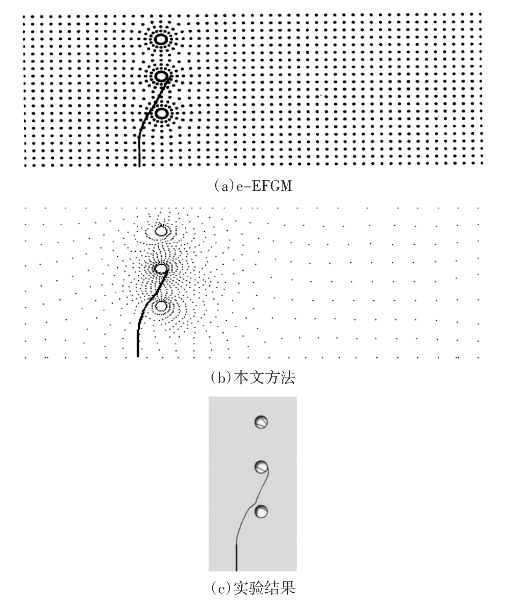
图6.20 e-EFGM、本文方法得到的裂纹扩展路径与试验结果[127]的比较(试样1)
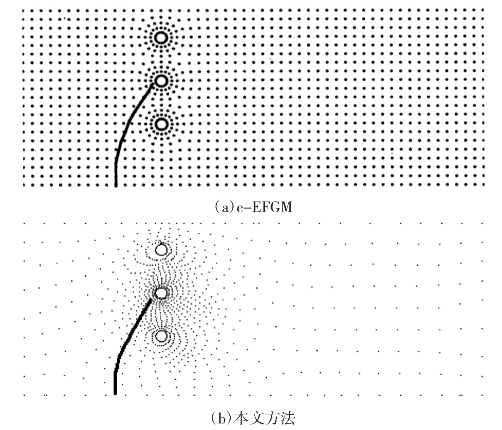
图6.21 e-EFGM、本文方法得到的裂纹扩展路径与实验结果的比较(试样2)